树脂砂球铁件表层球化不良原因分析及解决办法!
摘要 : 通过金相,发现铸件表面球化不良,异常组织为片状石墨层,厚度在3~5mm,而且在片状石墨与球形石墨之间存在一极薄蠕虫状石墨过渡区,如图1所示。通过资料,发现许多文献对采用树脂自硬砂工艺生产的球铁件表面出现的片状石墨缺陷进行了报道,说明这种缺陷是一种普遍现象。
济南海耀铸造生产各种铸件十余年,拥有丰富经验,让小编从海耀铸造的方面为您讲解一下球铁件表层球化不良原因分析。
铸件表层球化不良的主要原因是,高温下型砂中的S元素进入铁液,降低了铸件表层的残余Mg含量。要防止球铁铸件表层出现异常组织,必须阻止型砂中的S在高温下进入金属液。可以从三个方面解决这个问题:一是降低型砂中S元素的含量,减少传递源;二是采取措施,阻止S元素由型砂向铁液的传递,从传递过程上解决;第三则是增加铁水中残余Mg含量,抵消S 的影响。具体有以下几种方法:
减少传递源
降低再生砂的灼烧减量
再生砂中的硫元素与再生砂的灼烧减量有一定的比例关系。当灼烧减量高时,再生砂中S元素含量也高,在磺酸固化剂加入量以及型号不变的情况下,型砂中的S元素含量也会升高。高温下,S元素在砂型与铁液界面处浓度梯度随之增大,型砂中的S元素向铁液中扩散的动力也会增大,进入铁液中的S增多,渗入深度加深,表面球化不良加重。降低再生砂的灼烧减量不仅能降低型砂中的硫含量,还能降低型砂的发气量,降低铸件产生气孔的几率。
采用低硫磺酸固化剂
型砂中的硫元素,主要来自于磺酸固化剂。有研究表明,型砂中的S元素很难通过一般机械再生的方法降下来,控制源头是最好的方法。在再生能力一定的条件下,采用低S固化剂,能有效降低铸型和再生砂中的硫含量,从而从根本上解决表面层球化不良现象。
降低固化剂的加入量
固化剂的加入量直接影响着型砂的硬化速度。在满足初始强度要求的条件下,应尽可能的降低固化剂的加入量,不仅能降低铸型和再生砂中的硫含量,还能降低成本。降低固化剂的加入量,型砂硬化速度变慢,铸型的终强度能得到一定程度的提高。但是固化剂加入量不能太低,否则较短的时间内很难将其混匀,使得型砂强度分布不均匀,表面稳定性也差。
截断传递途径
阻硫涂料 :这里的阻硫是指在涂料中添加其他物质,如MgO。当硫元素以SO2、SO2-和SO32-的形式通过含有MgO的涂料层进入铁液时,能被涂料层中的MgO所吸收。
提高铸件的冷却速度:在使用冷铁提高冷却速度的情况下,铁液不与树脂砂接触, 而与冷铁接触, 凝固加速, 形成硬壳, 也在一定程度上避免了硫元素的渗入。
降低浇注温度:在保证不出现其他缺陷的情况下,尽可能降低浇注温度。降低浇注温度, 能减少硫元素与液态金属的接触时间,减少硫元素的扩散,消弱球化衰退效果。
采取措施
增加灼烧减量和再生系统的检测、检修力度,将灼烧减量降至2%以下。此时再生砂中的S含量约在0.05%左右,在很大程度上降低了型砂与铁液界面S元素的扩散动力。
降低浇注温度,将浇注温度降至1350℃以下,减少S元素与液态金属的接触时间, 减少硫元素的扩散。
提高残余Mg含量,将残余Mg由0.03~0.04%增加到0.04~0.06%。
如果您有任何的需求,随时拨打我们的联系电话:0531-81216029。期待你的合作!
上一篇:超实用的树脂砂造型工艺参数大全,赶快收藏吧!2020-04-28
下一篇:铸钢件的浇注系统你了解吗?2020-04-29
【推荐阅读】:
责任编辑:海耀铸造
版权所有:http://www.jnhaiyao.com 转载请注明出处
我要评论: | |
*内 容: |
|
验证码: |
|
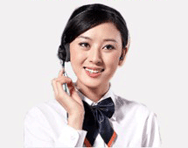
济南海耀新能源设备有限公司
免费咨询:13906406772
公司邮箱:861755503@qq.com
总部地址:济南市商河县经济技术开发区力源街东首
共有-条评论